Inside a Cardboard Box Factory: Where Packaging Comes to Life
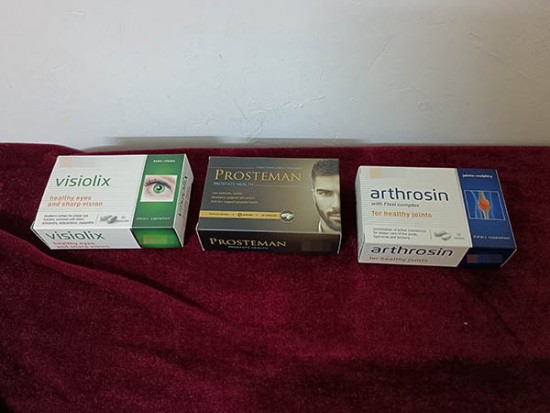
Cardboard boxes are everywhere. From shipping goods around the world to protecting your online orders, they play a crucial role in modern logistics and commerce. But have you ever wondered how they’re made? Step inside a cardboard box factory, where raw paper is transformed into strong, customizable packaging used across countless industries.
The Role of a Cardboard Box Factory
A cardboard box factory specializes in manufacturing corrugated boxes used for packaging, shipping, and storage. These boxes are made from sheets of paper-based material called corrugated board, which consists of a fluted inner layer sandwiched between two flat linerboards. This structure gives the box its strength, flexibility, and lightweight characteristics.Factories cater to a wide range of businesses—from e-commerce companies and food producers to electronics manufacturers and retail stores—by designing and producing boxes that meet specific size, strength, and branding requirements.
The Manufacturing Process
1.Raw Material PreparationIt all starts with large rolls of paper made from recycled fibers or virgin wood pulp. These rolls are the base materials for the corrugated board. Factories often source paper from integrated paper mills or external suppliers.
2.Corrugating
The paper passes through a machine called a corrugator, which heats, presses, and molds it into the fluted (wavy) shape. This fluted paper is then glued between two flat sheets to create corrugated board.
3.Cutting and Printing
Once the board is formed, it moves to cutting machines that shape it into the desired box style—regular slotted containers (RSC), die-cut boxes, or custom designs. At this stage, factories can print logos, handling instructions, or marketing messages directly on the cardboard using flexographic printing.
4.Folding and Gluing
The cut and printed boards are folded into shape and glued or stitched at the seams. Some boxes are left flat and bundled for easy shipping, while others may be pre-assembled.
5.Quality Control and Packing
Each batch goes through quality checks to ensure proper dimensions, strength, and print quality. Once approved, the boxes are bundled, palletized, and sent out for delivery to customers.
Customization and Innovation
Modern cardboard box factories don’t just produce plain brown boxes. They offer a variety of customizations including:●Custom sizes and shapes
●Full-color printing and branding
●Eco-friendly coatings and materials
●Reinforced structures for heavy-duty use
Factories also invest in technology like CAD software and automated cutting machines to create innovative packaging solutions that meet specific client needs.
Sustainability Focus
Today’s box factories are highly focused on sustainability. Most cardboard boxes are made from recycled materials and are themselves 100% recyclable. Many factories follow eco-friendly practices, such as using water-based inks, minimizing waste, and optimizing energy consumption.
Conclusion
A cardboard box factory may seem simple, but it’s a hub of precision engineering, innovation, and environmental responsibility. These factories ensure that products around the globe are safely delivered every day, wrapped in packaging that's both practical and sustainable.